Revamping
Repair of refractory brickwork of coke ovens under conditions of operating facility.
Concord Group has a high level of expertise in providing complex and specialized coke oven repair services under conditions of operating facility
- repair of refractory brickwork of coke ovens using the innovative method of ceramic welding;
- repair of refractory brickwork with one-sided, two-sided and through-wall re-bricking of a group of heating walls;
- preventive repairs of the walls of ovens chambers and soles;
- repair of the lower structure of coke batteries, including flues and grates;
- repair of the top of coke oven batteries with replacement of lining, charging hole frames, coke oven gas burners, etc.;
- lining of ovens equipment;
- repair of brickwork above and below flash plates;
- insulation and sealing of front walls of regenerators, gas-and-air boxes;
- adjustment work for the heating system of coke oven batteries;
- repair of bracing equipment of coke oven batteries;
- repair of movables machines;
- repair of equipment of by-product plants for desulphurization and trapping;
- complex repair of units of the dry coke quenching unit;
- repair, lining, cleaning of process pipelines and gas pipelines.
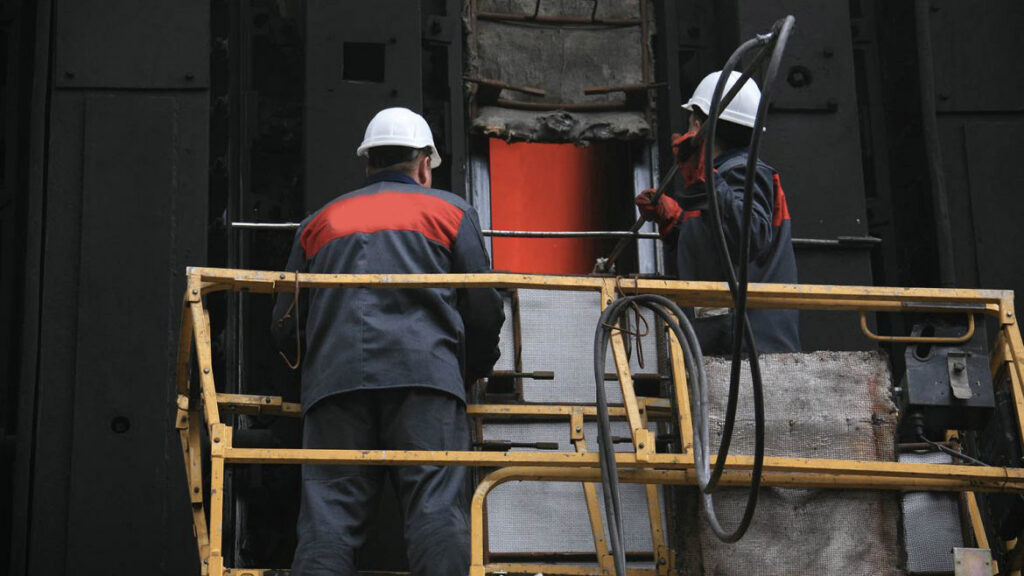
Ceramic welding is one of the most effective ways to repair the refractory lining of thermal units, aimed at extending and increasing their service life.
A distinctive feature of the ceramic surfacing method is that due to the release of heat during the combustion of the fuel component of the mixture in an oxygen environment, the refractory components of the mixture are melted and the damage to the masonry is filled. The applied material is similar to refractory brick in its crystal structure and physico-chemical parameters. When the melt solidifies, a structure is formed with a ceramic bond between the masonry material and the coating.
This method of repair ensures the rhythmic operation of thermal units, a reduction in the consumption of expensive refractory bricks, and a reduction in the number of labor-intensive “cold” repairs associated with the replacement of refractory masonry.
ADVANTAGES OF USE OF CERAMIC WELDING:
- repair without stopping the production process;
- instant fusion of the deposited material with repairable refractory masonry;
- extending the life of coke oven batteries.
- “Hot” repairs of refractory masonry (temperature in adjacent walls and not shifted verticals is not lower than 800°С);
- Repairs of refractory masonry with partial or complete re-laying of piers (temperature in adjacent piers is less than 300°C).
- Complete rearrangement of coke oven batteries in the same dimensions.
- one-sided repair of individual piers to a depth of up to 4 verticals;
- two-sided transfer to a depth of up to 4 verticals;
- complete rearrangement of individual piers. Engineering solutions for thermal insulation and ventilation of the working area make it possible to carry out hot repairs of refractory masonry all year round in any climatic conditions
- in-line 2-sided repairs to a depth of 8 verticals of piers and walls of regenerators;
- relocation of individual walls and regenerators;
- laying of piers and regenerators by the flow-group method;
- re-laying of the upper structure of the furnaces with a possible partial repair of the walls of the regenerators and cooling of the entire battery.
- coke batteries for the production of blast-furnace and commercial coke;
- furnaces for the production of special types of coke and heat treatment of carbonaceous and other materials